We can briefly list the main advantages and superior features of Plastic Manholes as follows;
- Sealing
- Resistance to Chemical Effect
- Plastic - Plastic compatibility
- Flexibility
- Resistance
- Low Weight
- Ease of Assembly
- Long lasting
- Maintenance free
- Economically beneficial
- Recyclability and Environmental Harmlessness
“It has high resistance to water and chemicals. It protects the environment with its sealing feature. Plastic manhole-Plastic pipe is connected in a way to completely prevent leakage.”
Due to its plastic structure, it has internal and external sealing properties. Here, the product’s resistance to chemicals comes to the fore. Examination chambers can be manufactured as a single piece or consist of units. In other words, it can also have a modular structure. In this case, perfect combination and sealing is achieved as a result of the perfect “Plastic – Plastic compatibility” between the units and the compatibility with plastic-based sealing elements.
In addition, the inlet-outlet channels that provide the connection to it also maintain leak-tightness by making connections within the plastic fit. Unused channels can be perfectly closed with a simple element and easily put into use whenever desired.
The result provides a huge advantage in both aspects. It protects the system it belongs to by not letting in groundwater and chemicals and prevents unwanted materials from mixing into the system. It facilitates maintenance by ensuring that the examination chambers remain clean. It prevents damage to communication lines and joints in telecommunications. It protects the natural balance by preventing harmful materials from mixing with the nature in wastewater carrying systems.
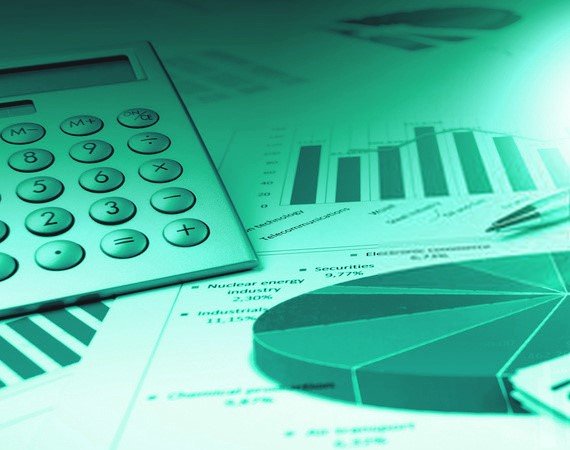
“Plastic Manholes are Flexible and Strong”
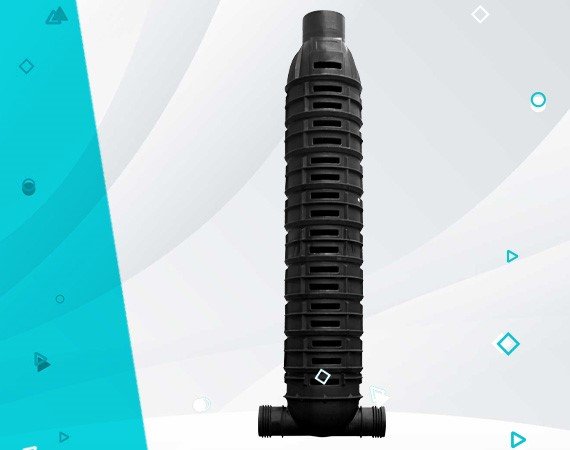
Today, 95% of the materials used in the natural gas, drinking water and sewage systems of developed countries are plastic-based. Polyethylene elements are more durable, practical and economical compared to other elements, depending on their usage areas. Resistance to ground movements is the most important issue to be taken into consideration, especially in infrastructure works in the earthquake zone. When underground structures, which are indispensable parts of daily life such as drinking water and sewage lines, natural gas and oil pipelines, tunnels, electricity and communication lines, are out of use even for a short period of time, it negatively affects daily life.
Plastic is the only material class that emerged from infrastructure systems with zero damage, especially during the 1995 Japan (Kobe) earthquake and the 1999 Turkey Gulf earthquake. After the great earthquake in our country in 1999, all infrastructure lines except “natural gas service lines” were damaged. The reason for this was that only the natural gas lines were laid with Polyethylene elements. In the renovation works carried out after the earthquake, Turkish Development Bank constructed the entire drinking water infrastructure in this region using Polyethylene (PE) elements.
“Plastic Manholes weigh approximately 5% of concrete manholes. 2 people can easily install them with light equipment. They are very suitable for use in difficult conditions and terrains. The installation time is very short. The application area is restored in a short time.”
The biggest advantage of the product in transportation and assembly is its low weight. As it is known, infrastructure applications are carried out regardless of location within the city or outside residential areas.
The first problem here is transportation. Traffic laws and application location conditions are determining factors in vehicle tonnage. As a result of the research conducted especially on our project product, it is seen that the weight of the Reinforced Concrete Building Element is approximately 18 times the weight of Thermoplastic Building Elements of the same size.
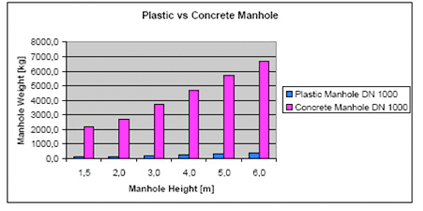
One of the most important elements during the assembly phase is time. The basic principle in infrastructure applications is to carry out the application quickly, cover the structure as soon as possible and bring the region back to its former conditions. Especially in the renewal of existing infrastructure systems, the work areas are generally within residential areas and include areas where there are people and traffic, and the application must be done very quickly in terms of both security and environmental disturbance.
Compared to the concrete element, the Thermoplastic Element can be assembled in a very short time and its connections can be activated in a similarly fast and, more importantly, safe manner (sealing, etc.).
“The average lifespan of Plastic Manholes is thought to be 50 years. It does not require maintenance throughout its life.”
The fact that infrastructure projects have started to be carried out on a long-term and continuity basis rather than daily has increased the need for maintenance and the importance given to this requirement. In the adaptation and improvement of existing infrastructure systems in the light of new projects, maintenance, in fact, major repair and renewal is involved.
Infrastructure work of institutions and companies providing energy, telecommunications and other information technologies is accelerating. Because the sector is constantly developing and the number of areas and people served is increasing. Institutions and companies that provide this service make significant investments because they have to improve their service quality. The fact that their investments last a long time and they want to get a return on their investments without any problems has increased the importance they attach to maintenance.
Considering the work and reports of the maintenance and repair teams, damage and maintenance requirements come to the fore, especially in concrete inspection rooms.
It is a very long-lasting material due to its plastic structure. It has a maintenance-free structure within the framework of all the features we have mentioned.
“Plastic Manholes provide price advantage in the long term with their superior features.”
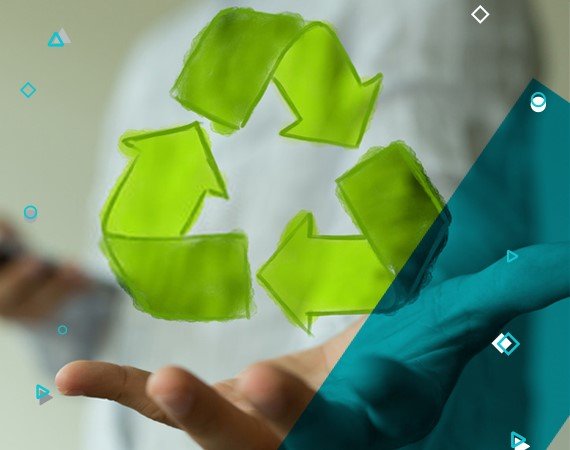
The fact that Plastic Manholes are long-lasting and do not require maintenance, while the concrete product currently on the market is short-lived and in need of maintenance, as mentioned, highlights the Economic Advantage of Thermoplastic Infrastructure Elements.
“The greenhouse gas emission of Plastic Manholes is 2kg / year CO2.”
Developed countries are trying to rapidly reduce CO2 levels. In the analysis made using the Life Cycle Assessment Method:
If the leakage is ignored, the Concrete Building Element produces 33.43 kg/year CO2 as Greenhouse Gas emission during the production, transportation, maintenance and service processes, and Thermoplastic inspection units produce 2.42 kg/year CO2 in the same process, which is a rate of about 10%. If leakage is taken into account, it is stated that these values increase to 423.38 kg/year CO2 for concrete, while they remain the same in thermoplastic inspection units and are 2.42 kg/year CO2, and it is emphasized that this is approximately 175 times higher.
In addition, Plastic Manholes are 100% recyclable.